Opening the Power of Welding WPS: Strategies for Efficiency and Safety And Security in Fabrication
In the world of manufacture, Welding Treatment Requirements (WPS) stand as the foundation of welding operations, dictating the required steps for attaining both effectiveness and safety in the manufacture procedure. Recognizing the ins and outs of WPS is vital to utilizing its full potential, yet several companies have a hard time to open real power that lies within these files (welding WPS). By delving right into the approaches that maximize welding WPS, a world of enhanced performance and enhanced security awaits those willing to discover the nuances of this important facet of manufacture

Importance of Welding WPS
The importance of Welding Treatment Specs (WPS) in the fabrication sector can not be overstated. WPS serve as an essential roadmap that describes the necessary steps to guarantee welds are performed continually and properly. By defining crucial specifications such as welding processes, products, joint designs, preheat temperature levels, interpass temperatures, filler steels, and post-weld heat therapy demands, WPS give a standardized approach to welding that boosts performance, high quality, and safety in construction processes.
Adherence to WPS assists in achieving harmony in weld quality, minimizing the likelihood of flaws or structural failures. This standardization additionally helps with conformity with industry regulations and codes, ensuring that produced frameworks meet the needed safety and security standards. Additionally, WPS documentation allows welders to reproduce successful welding procedures, bring about consistent results throughout various projects.
Fundamentally, the thorough development and stringent adherence to Welding Treatment Specifications are critical for maintaining the honesty of welded structures, securing against potential threats, and promoting the online reputation of construction firms for supplying top quality services and products.
Secret Components of Welding WPS
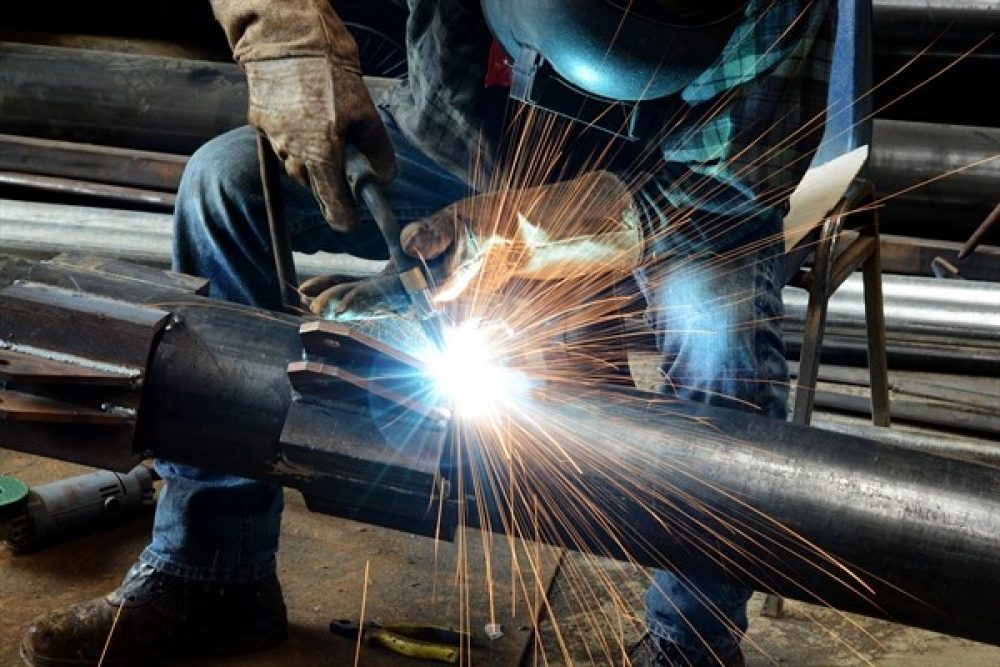
Enhancing Effectiveness With WPS
When optimizing welding procedures, leveraging the essential components described in Welding Treatment Specs (WPS) comes to be vital for making best use of and streamlining processes performance. One way to enhance performance with WPS is by thoroughly picking the ideal welding criteria. By sticking to the particular standards provided in the WPS, welders can make sure that the welding devices is established correctly, resulting in consistent and top quality welds. Additionally, adhering to the pre-approved welding series outlined in the WPS can substantially decrease the time invested in each weld, ultimately enhancing general performance.
On a regular basis reviewing and updating the WPS to include any lessons discovered or technical advancements can likewise add to effectiveness improvements in welding procedures. By embracing the standards established forth in the WPS and continuously looking for ways to maximize processes, makers can attain greater efficiency levels and remarkable end outcomes.
Ensuring Safety And Security in Fabrication
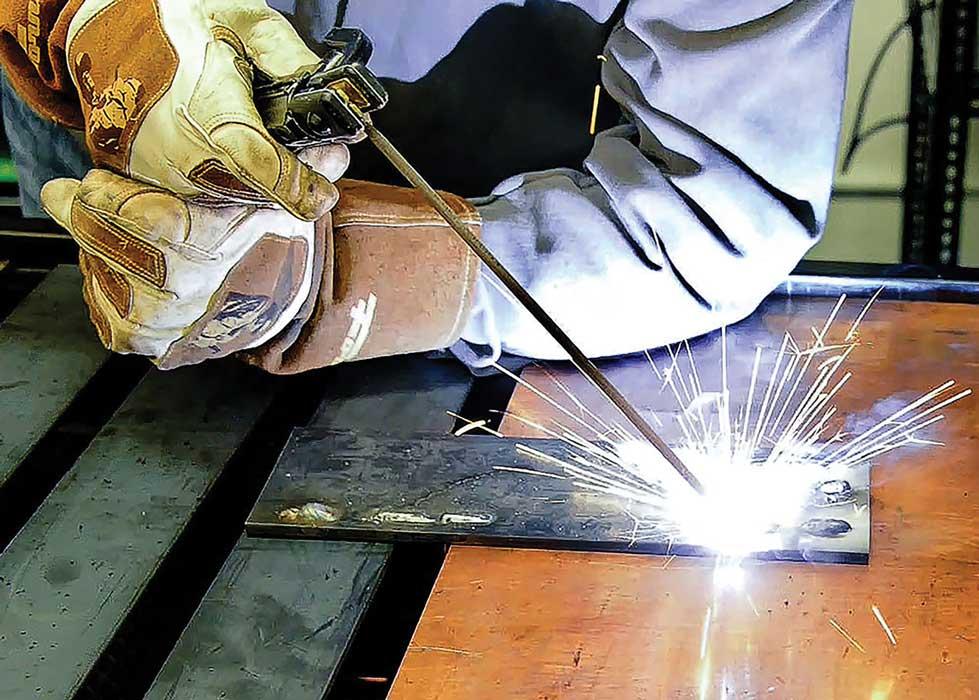
Safety methods in manufacture play an essential role in safeguarding personnel and maximizing functional procedures. Ensuring safety in fabrication involves a complex method that encompasses different aspects of the welding process. One fundamental aspect is the stipulation of personal protective tools (PPE) tailored to the specific dangers existing in the construction atmosphere. Welders should be furnished with suitable equipment such as headgears, handwear covers, and protective apparel to reduce dangers linked with welding tasks.
In addition, adherence to appropriate ventilation and fume removal systems is important in maintaining a healthy workplace. Welding fumes include harmful materials that, if inhaled, can pose severe health and wellness risks. Implementing effective ventilation procedures assists to decrease exposure to these harmful fumes, advertising respiratory health and wellness amongst employees.
Routine tools upkeep and evaluations are likewise essential for guaranteeing security in fabrication. Malfunctioning machinery can result in mishaps and injuries, highlighting the importance of routine checks and timely repair services. By prioritizing precaution and fostering a culture of awareness, fabrication facilities can develop a safe and effective workplace for their employees.
Applying WPS Ideal Practices
To improve operational effectiveness and make certain quality results in construction processes, integrating Welding Treatment Requirements (WPS) best techniques is critical. Selecting the proper welding process, filler material, and preheat temperature specified in the WPS is critical for attaining the preferred weld quality. Ensuring that qualified welders with the required accreditations lug out the welding procedures according to the WPS standards is click over here now essential for consistency and reliability.
Conclusion
In conclusion, welding WPS plays a critical function in making sure effectiveness and security in manufacture procedures. By concentrating on crucial elements, improving effectiveness, and applying best practices, business can optimize their welding procedures. It is important to prioritize security actions to avoid mishaps and make sure a smooth manufacturing procedure. By complying with these methods, businesses can unlock the full possibility of welding WPS in their manufacture procedures.
In the world of construction, Welding Treatment Specs (WPS) stand as the foundation of welding procedures, determining the needed actions for accomplishing both effectiveness and security in the construction procedure. By defining essential specifications such as welding processes, products, joint styles, preheat temperatures, interpass temperatures, filler steels, and post-weld warmth treatment needs, WPS give a standard method to welding that my review here boosts performance, high quality, and safety in fabrication procedures.
When optimizing welding operations, leveraging the essential aspects outlined in Welding Procedure Specifications (WPS) ends up being necessary for simplifying processes and optimizing efficiency. (welding WPS)